A New Take on Timber
Whitefish business receives grant to study new method of developing cross-laminated timber and other engineered-wood products
By Molly Priddy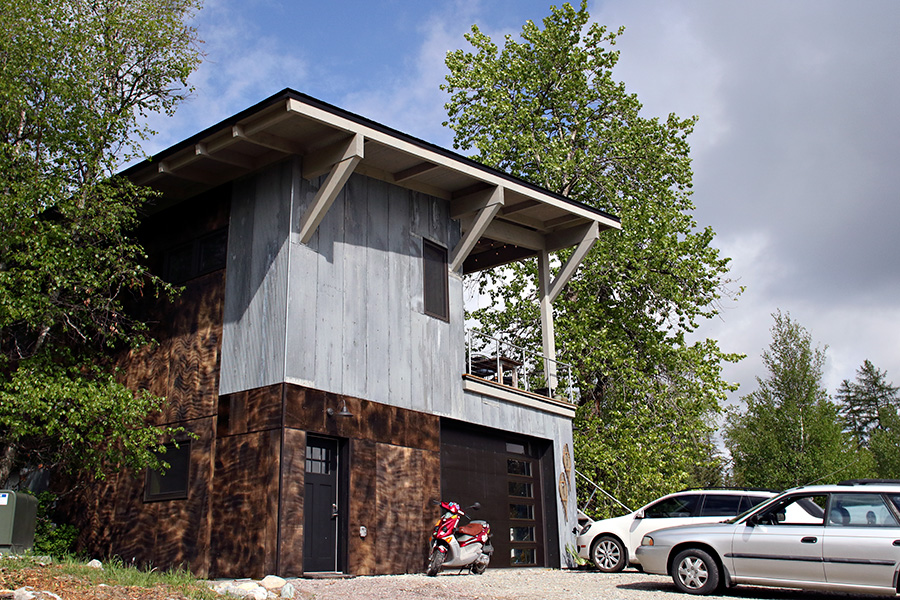
WHITEFISH – From the outside, the house looks like a modern addition to the farmland, a modest, two-storied building with a slanted roof; the wood and metal visible give it a clean feel, but nothing too different from other homes in the valley.
Then you get closer – inside-the-walls closer.
The walls that are at least a foot thick, with a layer of cross-laminated timber, wood-fiber insulation, and another layer of engineered wood underneath the metal siding, all lying on top of a 1,000-square-foot concrete slab.
Patrick Clark, who owns Wooden Haus Supply with his brother Ron Clark, said that after months of planning and using 3D digital mapping that the actual building process of this house was extremely quick: it took two carpenters, one crane, and 10 hours to get it assembled.
“This house will be here for a couple hundred years,” Patrick Clark said, “unless they decide to disassemble it and move it or easily pop on some additions.”
While using cross-laminated timber (CLT) is a common building practice in Europe, the engineered wood product is still catching on in the United States. In Columbia Falls, SmartLam is running one of the first CLT production facilities in North America, whereas builders in Austria have been studying and using CLT for residential and commercial building for decades.
The benefits include high efficiency, longevity, minimal upkeep, and using a renewable resource – wood – instead of steel. The building style also removes the need for drywall in many cases, because the CLT is not only structural, but also the inner finish of the home.
The Clarks have spent eight years building relationships with builders overseas to learn more about such engineered wood products, and recently received a Wood Innovation Grant from the U.S. Forest Service to continue developing and studying a new method of using smaller diameter trees and lumber for CLT projects.
Typically, CLT projects use 2-x-6 or 2-x-8 planks, meaning trees that can produce those diameters are in high demand. And while that’s good for the sawmills’ bottom lines if they have such product in stock, the forests are still full of smaller trees.
“We wanted to figure out how to make CLT from really small pieces of wood, making the product fit the forest,” Clark said. “[We’ve found a way] to make these products out of the small-diameter timber that needs to come out of the forest.”
Clark’s proposal was one of 34 projects to receive federal funding totaling $8 million. The grants come from the U.S. Department of Agriculture’s attempts to expand and accelerate wood products and wood energy markets. For example, previous grants supported the successful blast testing of CLT, which allowed the Department of Defense to use it for on-base hotels, while another grant allowed researchers to perform a feasibility analysis for new CLT facilities in the U.S.
Sawmills also aren’t typically outfitted to process the size of trees needed for the Clarks’ project, but they’ve developed equipment the mills could use.
“We would put the equipment in and they would harvest the timber,” Clark said.
The home, which belongs to Jake Christiansen and Yvonne May, is outfitted with European-style, triple-paned windows, and the living area sits atop a heated shop. They kept the temperature around 70 degrees, and the building is so energy efficient with the wood that their entire heating bill for January was $42.
Using CLT meant they could have a smaller foundation footprint, which consists of two feet of drain rock under six inches of foam insulation under eight inches of concrete.
“That saved about $10,000,” May said.
Clark also stripped out other unnecessary expenses from the project, including steel beams.
In sum, it took two-and-a-half months to build and finish out the house. The wall panels, which are all single pieces, were imported from Austria because their CLT is not only functional, but architectural level as well, whereas American CLT is still structural without the fine finish.
This is the couple’s second CLT house, and they’re already working on a third, excited to use the new information they learned building this house. They, along with the Clarks, want to host educational meetings with builders and contractors and homebuyers to show what’s possible.
While it’s not necessarily a new technology, the Clarks hope to tailor CLT more to the forests’ ability to produce. Not only would their new idea get its wings, but the market would benefit.
“That gives sawmills the opportunity to be profitable,” Clark said.
For more information on Wooden Haus Supply, visit www.facebook.com/woodenhaussupply.