Growing Up Green
Vertical Greens aims to produce 10 acres’ worth of produce in a 320-square-foot space, providing fresh greens year-round
By Micah Drew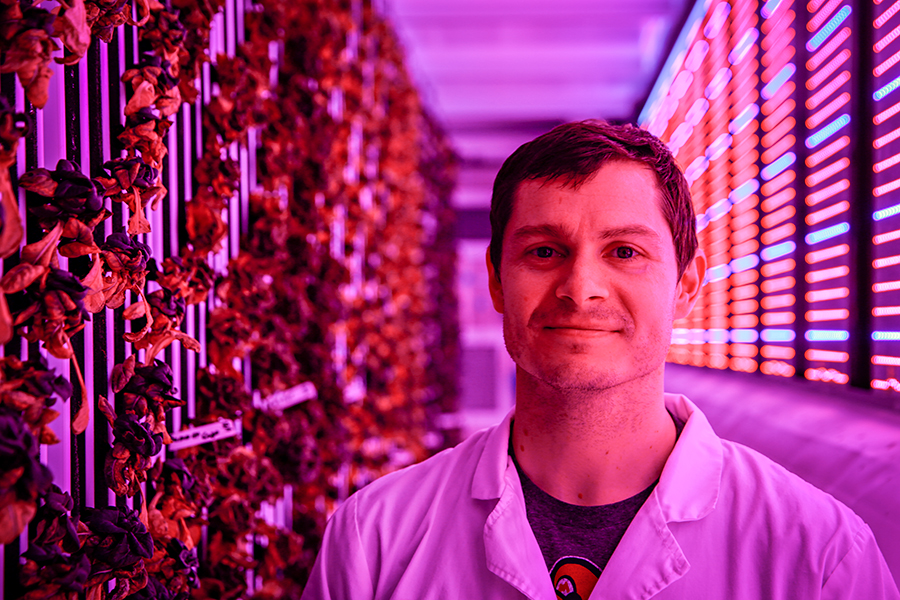
Amid a light January snowfall in Whitefish, Dustin Lang dragged open the metal door of a nondescript shipping container sitting in the driveway of The Farm at River’s Bend.
Inside, a blinding array of red and blue LED lights cast a violet glow on rows of hanging panels covered with a variety of salad greens.
The futuristic-looking garden is Vertical Greens, a fully contained hydroponic vertical farm that is the latest venture of recent Flathead transplant Tim Moyer.
“This is the perfect place for this kind of farm,” Moyer said, gesturing to the snowy landscape in Whitefish. “We could grow 10 acres’ worth of food right here on this little spot, and do it all year long.”
Moyer and his wife Harline moved to their property east of Whitefish a year ago after spending a decade running a 69-acre sustainable farm in Hawaii.
Their Hawaii operation, Laihana Family Farms, utilizes a large volunteer workforce, and several years ago a volunteer from New York City told Moyer about a increasingly popular farming technology — hydroponic container farms.
Since Hawaii has a year-round temperate climate, the idea of moving growing operations into a freight container didn’t seem necessary, but Moyer kept the idea in his head. A few months after moving to Whitefish, Moyer put the idea into action, and the first shipping container arrived in October.
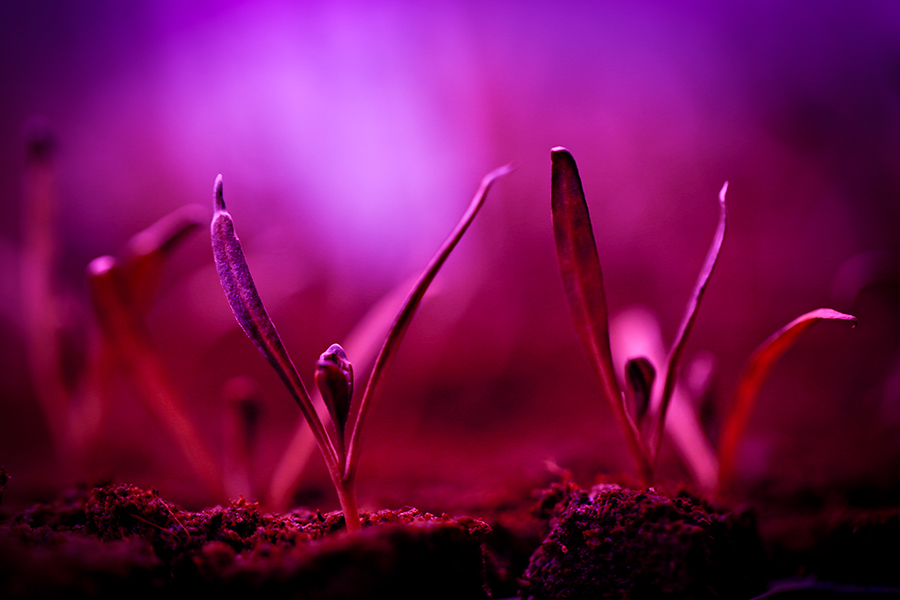
The company behind the shipping container pod is Boston-based Freight Farms, the first in the nation to manufacture and sell self-contained hydroponic farms. The 40-foot shipping containers, which take up a mere 320 square feet, can grow the equivalent of 2.5 acres’ worth of produce. Moyer plans on adding three more containers once his operation becomes economically sustainable.
Lang, a family friend of Moyers with an engineering background, handles the day-to-day running of the farm.
“The container showed up about a day after I did and it was just a pile of boxes and panels,” Lang said. “There was some assembly required.”
Once the growing systems were fully assembled, Lang planted the first lettuce seedlings and plunged into the world of hydroponic farming.
“We just hit the ground running,” Lang said.
The container has space for roughly 13,000 plants between the seedling nursery and the vertical cultivation panels. Each harvest cycle takes nine weeks and yields around 1,200 heads of lettuce a week.
The container has several shelves underneath a workstation that serves as the seedling nursery, which houses up to 4,600 seedlings at a time. After three weeks, the seedlings are transplanted to vertical growing strips, which hang from the container ceiling and utilize a drip irrigation system.
In both the nursery station and the cultivation area, thousands of miniature LED lights provide an exact combination of red and blue wavelengths of light to promote growth.
“I counted once — it was more than 98,000 of them,” Lang said, explaining that the red light is essential for stem and leaf growth while the blue promotes chlorophyll production and dark green foliage.
The entire system uses five gallons of water a day, and recycles any leftovers. The container is also fully wired to allow remote control through an app, so everything from temperature and humidity to soil pH and electrical conductivity can be monitored via Lang’s phone.
“The last thing I do before I go to sleep is check that everything’s fine, and the first thing I check when I wake up in the mornings is how the farm is,” Lang said.
Even though the system is fully automated and the growing space is precisely regulated, Lang said there was a learning curve to the process. The first harvest had more than a 50% loss from a combination of over-saturated plants, spacing issues and a touch of mildew.
“We haven’t seen those problems since, but at that point, it was a bit of a panic,” Lang said. “We had to figure out how to fix it immediately, because we knew we were going to have nine weeks with that particular harvest. We’ve made a lot of corrections since then.”
Even so, Lang says the expectation is for about a 20% loss per harvest, where plants either go bad or are too small.
The first Vertical Greens harvest was made in December, and all produce since then has been donated to local restaurants, including Kandahar. Moyer hopes to soon achieve high enough weekly yields to provide fresh greens to all interested local restaurants every day.
“Produce loses nutrients as they sit around, but we can literally deliver fresh lettuce the day a chef asks us,” Moyer said. “It’s not like farm to table; this is like kitchen to table, because we can basically deliver still growing greens to the kitchen.”
In the future, Moyer hopes to host pop-up dinners at the farm with local chefs using the farm’s produce.
During the summer months, there will be opportunities for visitors to come and picnic along the Whitefish River, which meanders along the edge of the property.
The main course of the picnic will be, of course, a ready-made, leafy green salad.
“If we could put a salad on everyone’s plate year-round, that would be the dream,” Moyer said.
For more information, visit www.h2ogreens.com.