Contractors Face Historically High Lumber Prices
High demand and low supply of lumber and building materials, combined with complicated transportation logistics and supply chain disruptions, are contributing to skyrocketing prices
By Maggie Dresser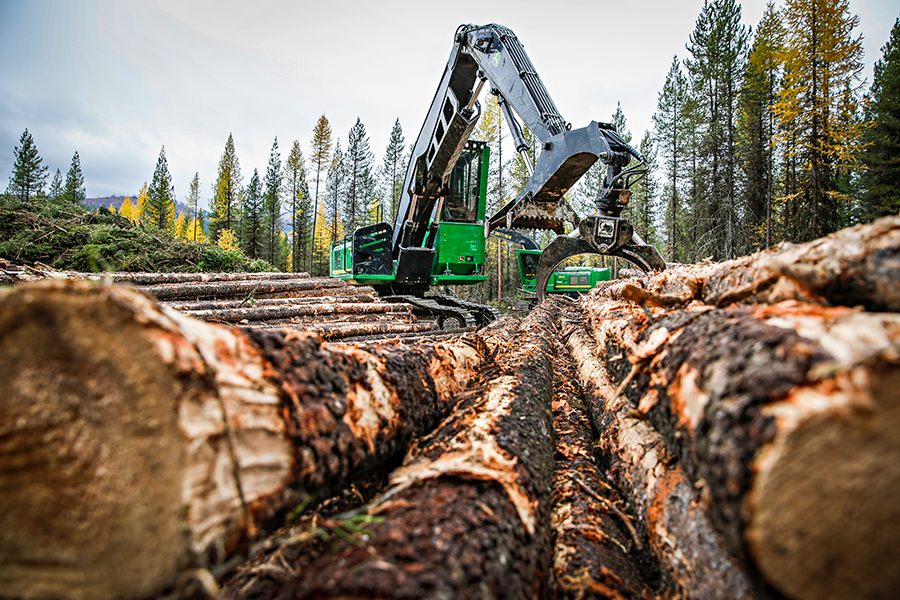
As an affordable housing general contractor, Edge LLC owner Layne Massie is struggling to reach his goal of bringing reasonably priced homes to the Flathead Valley as lumber prices in Montana continue to skyrocket, forcing him to increase new home prices.
The developer’s home prices have jumped an average of $40,000 to $50,000 more in the last year as lumber prices see historic highs.
“We are not able to build affordable housing anymore,” Massie said. “That’s kind of who we are and what we try to do for the most part … We’re still building and we’re still selling houses, but they’re not what I would call affordable.”
From the beginning of 2020, the lumber composite price index increased nearly 150% to a record high in September, according to recent report by the University of Montana Bureau of Business and Economic Research (BBER) in the Montana Business Quarterly.
Delivered log prices to mills were up 4% to 15% depending on the product from 2019, while lumber production was down 10.8% in 2020 compared to the year before, according to the report.
“The simple answer is the demand for lumber has been greater than the lumber being produced,” said Todd Morgan, the BBER Director of Forest Industry Research. “That’s the biggest piece of it, and I think the transportation piece is probably a bit clogged up.”
In the last year, the pandemic slowed down sawmill production nationwide, and while Montana’s mills weren’t as impacted by COVID-19, two of the state’s mills shut down for other reasons. Idaho Forest Group in St. Regis closed temporarily for a remodel and RY Timber Inc. in Townsend closed last summer, both unrelated to the pandemic.
Lumber transportation was also interrupted by the pandemic, leading to limited supply. Between a shortage of truck drivers, distribution center employees and added hassles of traveling across state lines, logistics were disrupted.
“A lot of facilities are saying, ‘We can’t get wood,’ manufacturers are saying, ‘We can get some wood but not a lot,’ and then there’s the labor challenge,” Morgan said. “The whole supply chain got massively disrupted.”
And with a shrunken lumber supply in the last year, the demand is increasing. Between new developments and home renovation projects, demand for wood products continues to grow.
At Edge, Massie is paying significantly higher prices for materials and has to plan far ahead without being too picky.
“We are getting what we need, but it’s a struggle to get them and there seems to be different products at different times,” Massie said. “It’s a lot more work to get our products … Our normal sources are not always able to provide us with what we normally need and we’re ordering weeks ahead of time.”
At Big Mountain Builders, a high-end residential construction company, owner Marc Daniels is experiencing similar difficulties and has to order lumber six to seven months in advance.
In the past year, his home prices have jumped roughly 30% to 40% because of spiked lumber prices. He says it’s pricing out his local clients, forcing him to put one project on hold, but he says out-of-area clients are still willing to pay top dollar.
“They’re willing to bite the bullet,” Daniels said. “They still want to move forward even though the price is so high.”
Montana’s lumber sales were up 15% in 2020, after adjusting for inflation, compared to 2019, according to the report.
Experts expect lumber and plywood demand to remain strong with historically high prices through 2021 as demand outpaces supply and interest rates remain low.
For decades, Morgan says sawmills have struggled to get enough logs and will likely focus on returning to a full-time and regular schedule in the future.
Programs like the Good Neighbor Authority, an effort between federal and state land agencies to collaborate with loggers for restoration and thinning projects, should help with wood supply, Morgan says.
“I think there’s opportunity to see forest management activities that will help generate wood,” Morgan said.
In the meantime, contractors are working to keep up with construction demand while planning far into the future to ensure they have all of the materials needed.
“Our demand has gone up drastically and we have a long waiting list,” Massie said. “We can’t keep up.”
“It’s really interesting times,” Morgan added.